Research
Development of a Virtual Force Sensor for a Low-Cost Collaborative Robot and Applications to Safety Control
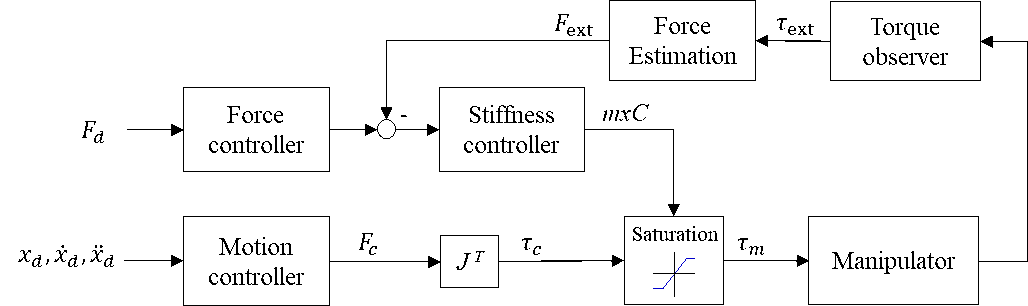
Developer: Shih-Hsiang Yen
CAD-based Offline Programming Platform for Industrial Robot-based Automation
Developer: Amit Bedaka
In manufacturing processes, programming robotic systems is a time-consuming, difficult and costly exercise, especially for small and medium-sized enterprises (SMEs). In this direction, many solutions have been proposed, to benefit with existing offline programming (OLP) software one needs to have a license. Further, the architecture of existing OLP solutions is rigid to modify or update with applications requirement. The goal of this research is to design and develop a customizable application-oriented offline programming (OLP) platform with flexible architecture, which allows integrate with other systems to generate novel systems. The core idea involves integrating CAD and robotics information to design and develop a virtual platform for 3D model importation, path planning, pose visualization, and robot script generation and modification within the same environment. The proposed approach based on OPEN CASCADE (OCC) open source libraries, which allow the users to independently develop and directly generate a robot path from CAD models. The platform fully utilizes geometric information from both the 3D object and the machine tool embedded in the CAD models and transforms them into the robot path required for an assigned task. This proposed platform offers friendly interaction in an intuitive way so that in a few minutes, any user can generate a robot path and visualize the simulation graphically. In addition, this innovative platform can help many industries achieve a higher level of intelligent automation and increase quality while reducing the cost of production.
--------------Past Projects--------------
Automatic camera calibration and image based object positioning systems based on 6-axis robot arm
Developer: Shao-Chun Li
This research provides two solutions to solve two exist problems in the automated production process. Firstly, we provide a solution to improve the efficiency and accuracy of a manual camera calibration process by using a robot-arm operated automatic calibration procedure. With the robot arm holding the camera in a predefined positions and orientation to take the pictures on the calibration board and calibrate the camera intrinsic parameters, the lens distortion parameters and hand-eye transform matrix at the same time in a fully autonomous manner. Secondly, in order to tackle the difficulty resulted from poor object positioning situations in the automated production process, we develop a new solution by attaching some artificial landmarks on the target object and using the camera system to perform the calibration based on the image containing the landmarks. In the case that the object has some position errors, the system can compute the compensation displacement needed by the robot arm by comparison of the two images of the artificial land marks. The results in the experiments show both systems have successfully shown high performance, high accuracy and high implementation potential.
Development of 6-axis Robot Autonomous Line Tracking and Following System
Developer: Tsung-En Hsieh
Pallet Box Autonomous Relocation System

Developer: Hsuan-Hung Chou
This study develops an autonomous pallet boxes relocation system that can fully automatically download boxes on the pallet and then relocate the boxes to designated locations. The system is based on the motion capability of a large robot arm and the computer vision modules that enable autonomous operation. The system comprises two sets of vision modules, one is Kinect v2 and the other is the stereo camera system, to serve in different workspace and requirement. The vision detection techniques developed in this system combine 2D image processing codes, and the points cloud algorithm. For detecting boxes with pattern surfaces, we use ORB(Oriented FAST and rotated BRIEF) feature detection and match template image features to the detected image so as to determine the box position and rotation. In order to determine the correct box position, we use RANSAC(Random sample consensus) and Homography matrix. For boxes without pattern features, we combine the 2D line detection to find the edge line of the box and remove the points on the edge line. After that, 3D clustering and OBB(Oriented bounding box, OBB)are implemented to obtain the precious positions of boxes and pallets. Then system will automatically calculate the path of the robot arm to pick the boxes and download them. In this system, there are three path planning options: first is to duplicate the stacking formation of the boxes on the original pallet to a new pallet, second is to allow the user to select the stacking pattern on a specific floor area, and third is to allow the user to define the size and the position of the target floor area, and the system will perform the optimized stacking pattern to save the space and time. The experiments have proven the system effective and precise, and with high commercial values.